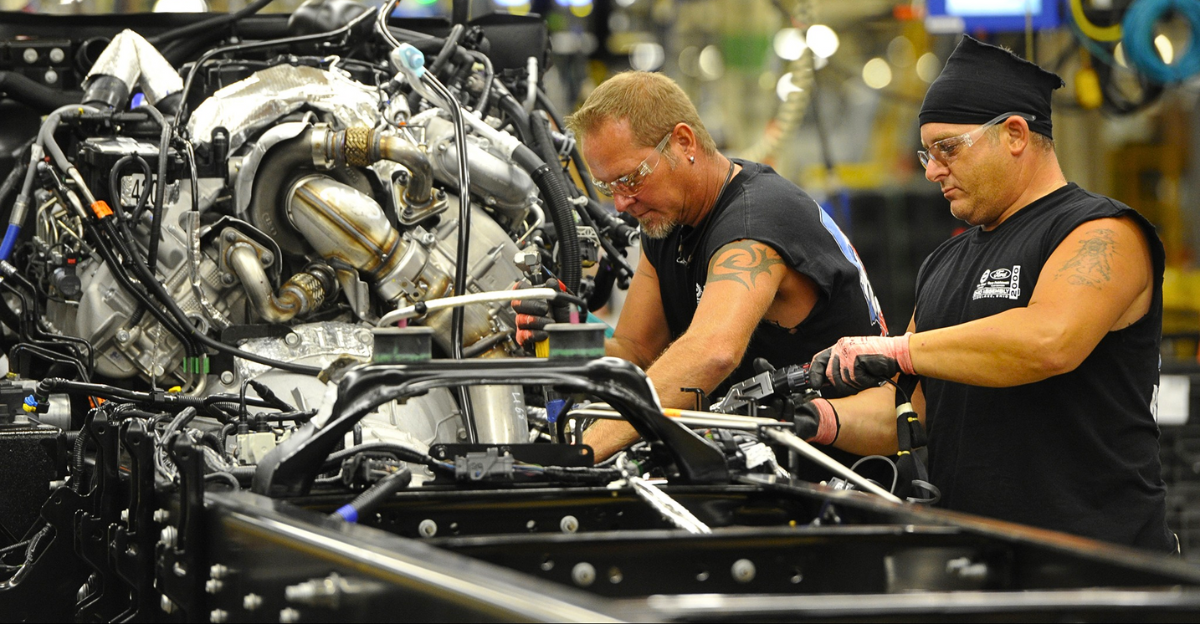
Ford Motor Company, a symbol of American manufacturing, faced a severe production crisis in 2025 due to critical shortages of rare earth minerals, key components in modern vehicle manufacturing. In May 2025, Ford temporarily shut down its Chicago Assembly Plant, halting production of popular models such as the Ford Explorer. CEO Jim Farley described the situation as operating “day to day” with “hand-to-mouth” supply management, highlighting the persistent and unpredictable nature of the crisis.
This disruption marks the latest blow to the automotive sector following the semiconductor shortage and the COVID-19 pandemic, underscoring the fragile global supply chains that manufacturers depend on. Farley’s candid admission signals unresolved challenges threatening Ford’s US production capabilities, impacting thousands of workers and local economies.
China’s Rare Earth Export Restrictions: The Root Cause
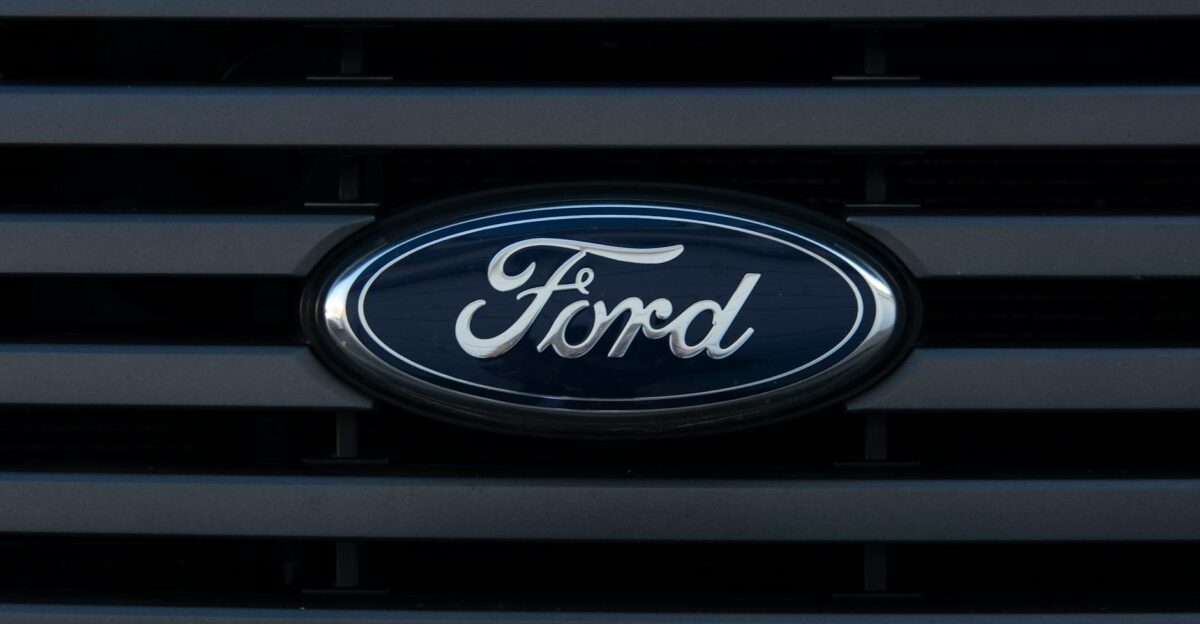
At the heart of Ford’s manufacturing halt lies the critical shortage of rare earth elements essential for components like power steering, audio systems, and electric motors. China, which controls over 90% of the world’s rare earth processing capacity, implemented stringent export licensing and regulatory changes in April 2025.
These new policies require automotive suppliers to submit extensive documentation, sometimes exposing sensitive intellectual property, and have approved only about 25% of license applications. The resulting bottlenecks have sent ripples through global automotive supply chains, leaving companies scrambling to source vital materials. This scarcity directly affected Ford’s ability to sustain production at its Chicago plant and other facilities.
Trade War Fallout Exacerbates Supply Disruptions
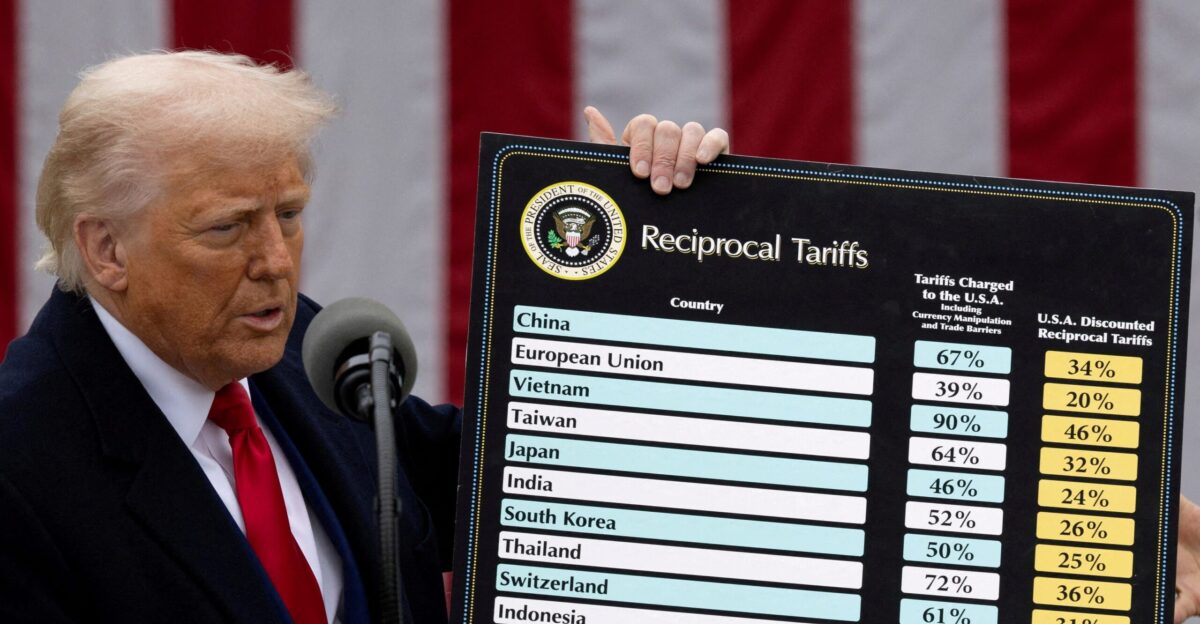
China’s export restrictions stemmed from escalating trade tensions with the United States, notably as retaliation against tariffs imposed during President Trump’s administration in early 2025. In response to a 25% tariff on imported automotive parts and vehicles, Beijing restricted exports of seven crucial rare earth elements.
This strategic move aimed to exert pressure during an already fragile trade standoff. The ripple effects extended beyond the US, impacting European manufacturers who report factory shutdowns due to depleted rare earth supplies. The automotive industry is thus caught in a prolonged geopolitical struggle, where trade policies have transformed into supply chain warfare, further complicating recovery efforts.
Industry Context: The High Stakes of Material Dependency
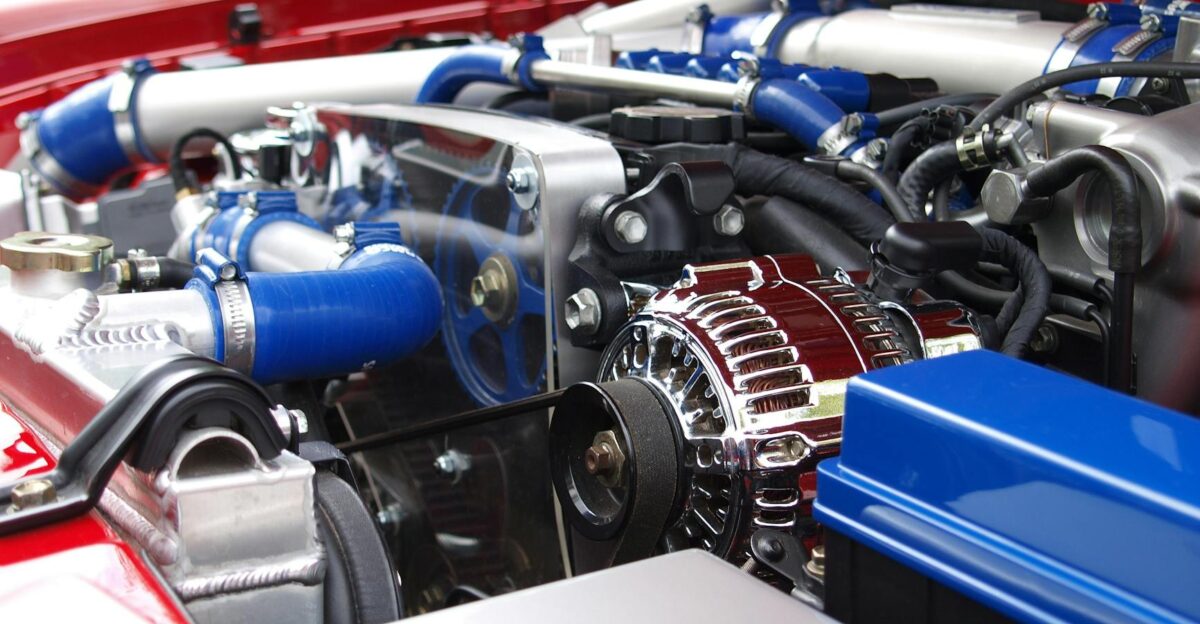
The current crisis has highlighted the automotive industry’s vulnerability to supply disruptions. Between 2020 and 2022, supply chain issues cost the sector over $500 billion in lost revenue. Rare earth magnets are critical for electric vehicles (EVs), powering permanent magnet synchronous motors, a technology featured in over a dozen upcoming models.
Ford’s Chicago Assembly Plant, which recently halted production, manufactures the Ford Explorer, one of the company’s highest-volume SUVs, and other models relying heavily on these materials. The shutdown thus represents a logistical setback and a substantial threat to future EV launches and profitability.
Production Halt and Its Human Impact
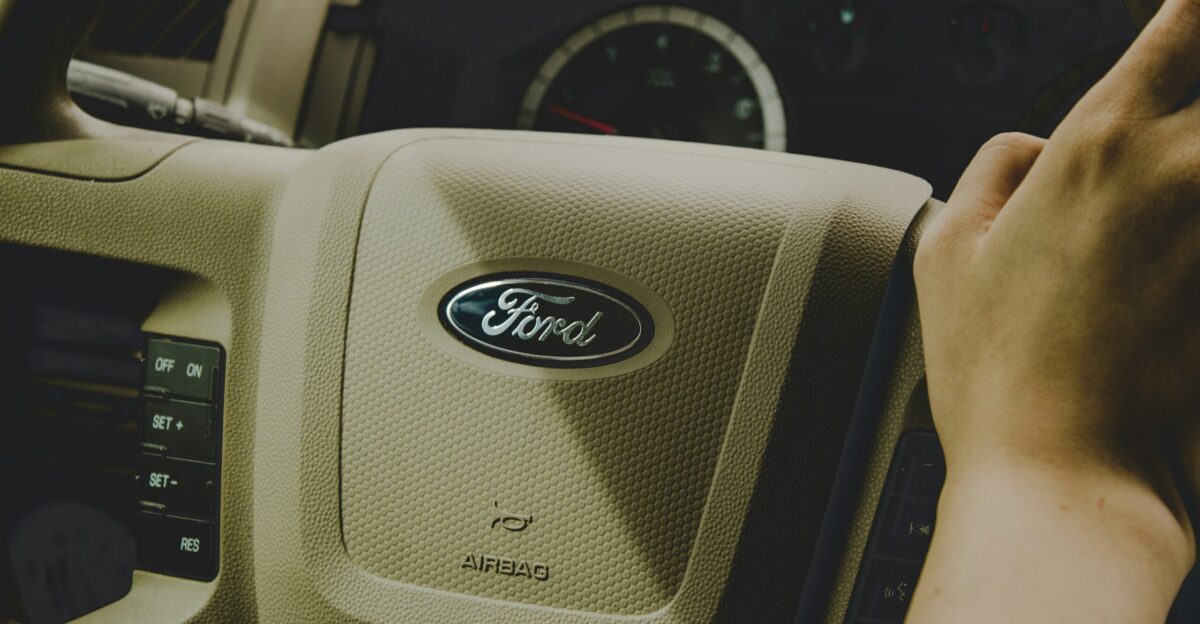
Here’s where it gets interesting: Ford’s decision to idle the Chicago Assembly Plant for a week in May is not just a story of supply chain woes; it has real people behind it. Approximately 4,600 workers at the plant faced immediate furloughs, with spillover effects causing layoffs at Ford’s nearby stamping facility, where 243 employees were let go.
Congressman Frank Mrvan highlighted in congressional hearings that the shutdown directly resulted from the mineral shortages affecting critical vehicle braking components. As one assembly line worker lamented, “One day we’re building cars, the next we’re wondering if we’ll have jobs next month.” These disruptions highlight the stark human toll of geopolitical and industrial challenges.
Meanwhile, European Suppliers Face Crisis
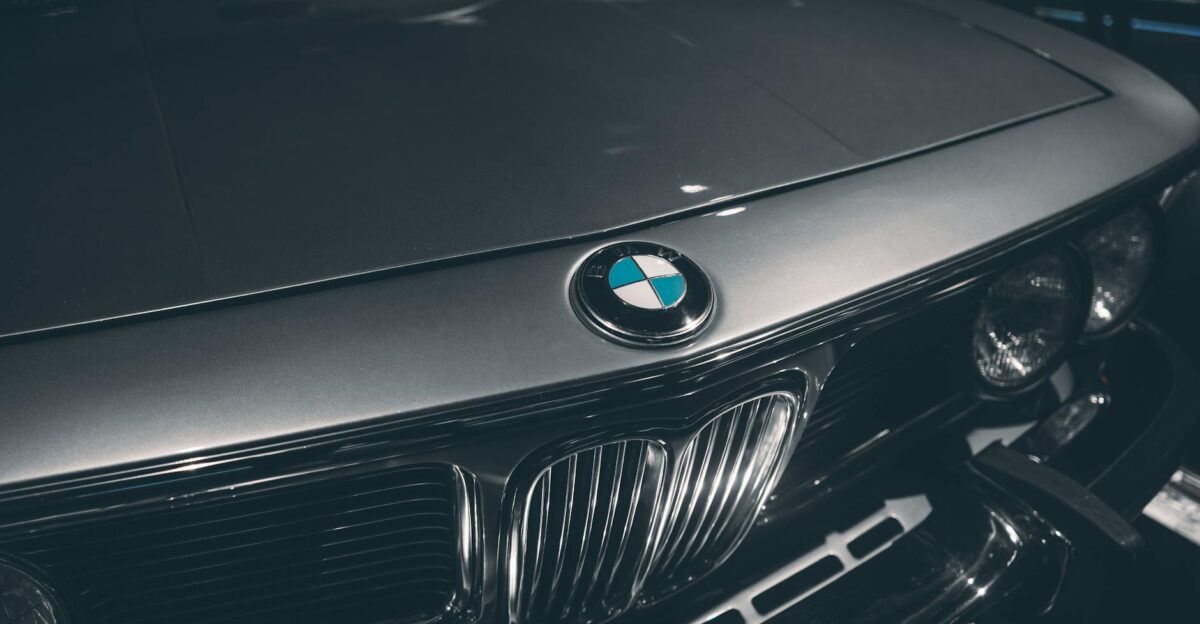
Across the Atlantic, European automakers are grappling with similar shortages. German magnet manufacturer Magnosphere described the situation as “full panic,” warning that production lines, including those at Volkswagen, Mercedes-Benz, and BMW, might soon halt if backup supplies fail to arrive.
Due to depleted rare earth stocks, European suppliers have already ceased operations in some areas. The pressure on manufacturers worldwide suggests a third major supply chain shock for the automotive industry in recent years, a strain that could reverberate across global markets and consumer availability for months.
Scrambling for Solutions: Diversifying Supply
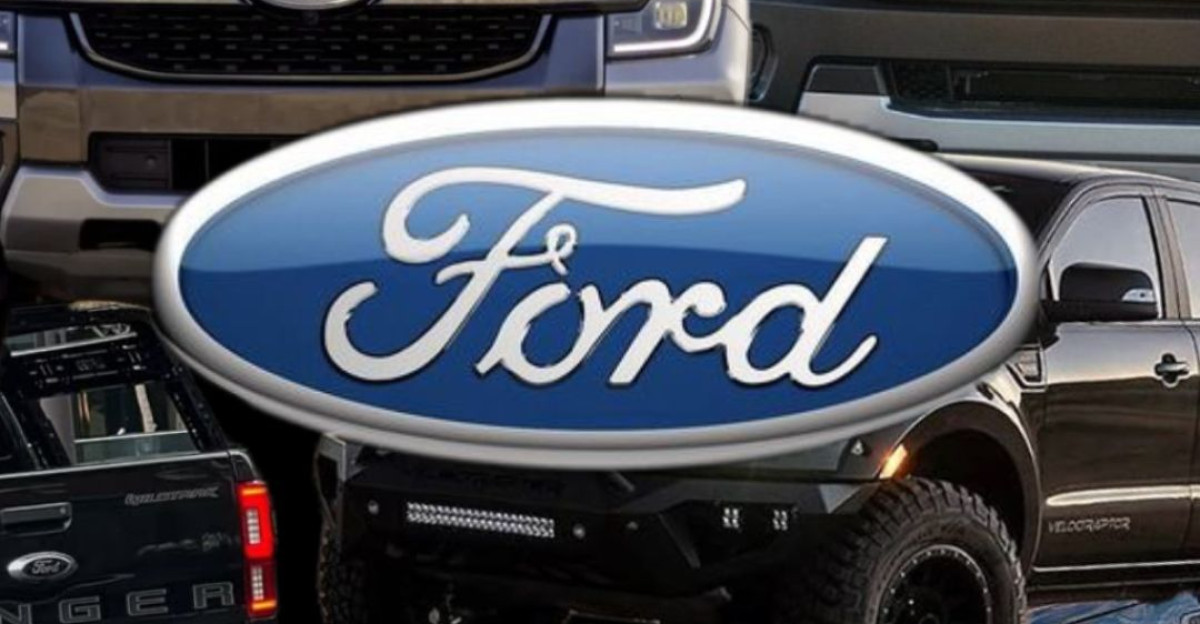
To mitigate the crisis, Ford and other automotive companies are urgently searching for alternative sources of rare earth materials beyond China. Suppliers in Vietnam, Indonesia, Japan, Australia, and the United States are under consideration to break the current dependence.
However, industry experts warn that existing inventories typically cover only 4-6 weeks of demand, making any prolonged shortage extremely disruptive. Ford is also actively lobbying the US government, emphasizing the importance of preserving Midwest manufacturing jobs tied to rare earth access, while working to forge direct supplier relationships to stabilize future operations.
Market Turbulence Amid Rising Disruptions
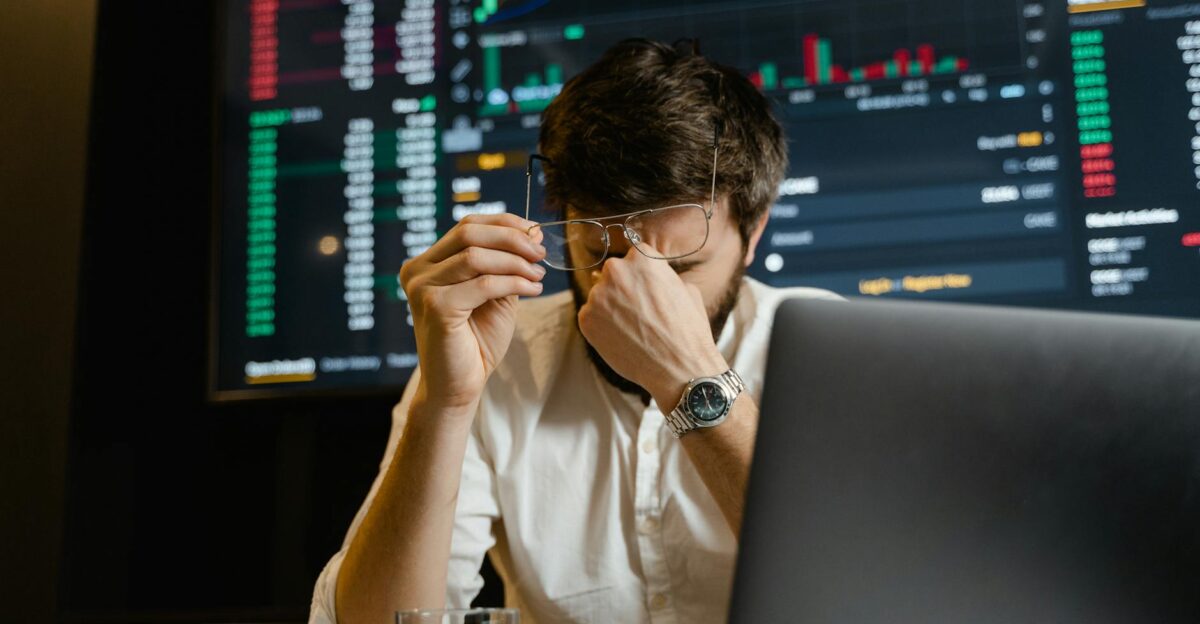
The supply chain challenges are part of a broader trend of increasing disruptions, with the automotive sector experiencing a 37% surge in incidents in 2024, including factory fires, protests, and extreme weather events. Despite these issues, companies report modest improvements in supply chain resilience, attempting to reduce order backlogs and increase inventory buffers.
Yet, the financial burden largely falls on suppliers, straining the production ecosystem further. Observers caution that unless geopolitical tensions ease and material flows normalize, the cost pressures will continue to impact vehicle prices and consumer availability.
A Glimmer of Hope: Diplomatic Progress
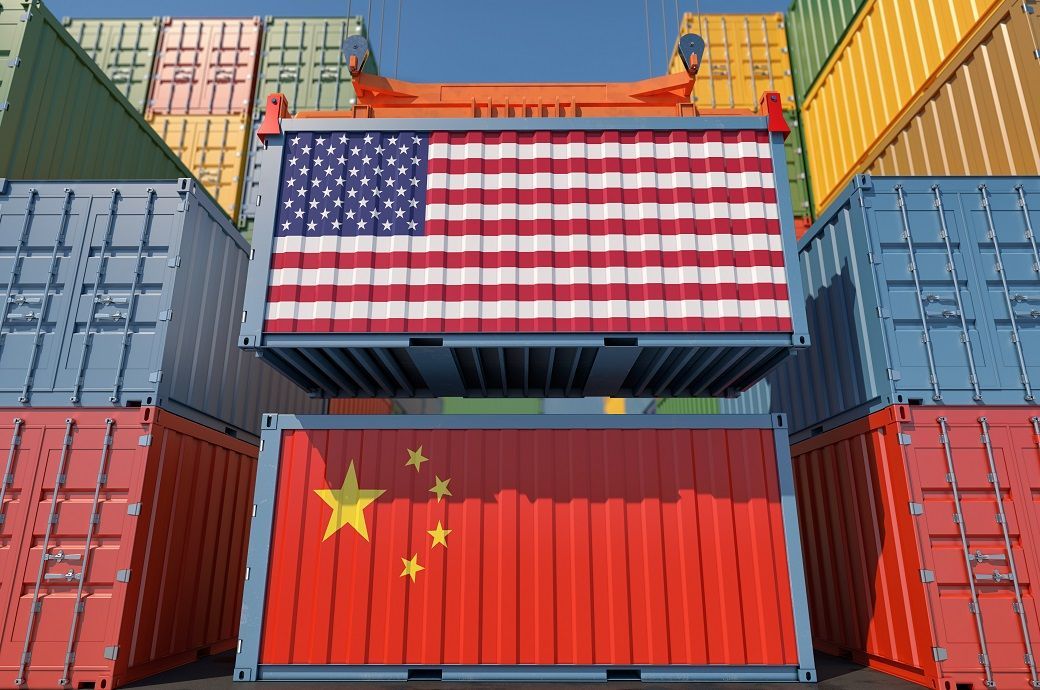
In a positive development, US and Chinese officials reached a tentative framework agreement in late June 2025 during talks in London. China pledged to expedite approvals for rare earth export licenses in exchange for the US lifting specific countermeasures. Commerce Secretary Howard Lutnick confirmed China committed to “deliver rare earths,” potentially easing months of supply chain disruptions. However, the details remain sparse, and industry leaders remain cautiously optimistic. For workers and communities affected by Ford’s shutdowns, this diplomatic breakthrough offers a hopeful, though tentative, path toward restoring production stability.
This unfolding saga of Ford’s manufacturing challenges underscores the fragile intersection of global trade policy, resource dependency, and industrial resilience. It reminds us that the fate of iconic American factories rests not only on the assembly line but also on geopolitics and supply chain strategy.